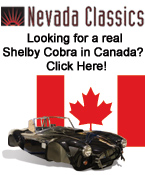 
Main Menu
|
Nevada Classics
|
Advertise at CC
|
S |
M |
T |
W |
T |
F |
S |
|
|
|
1 |
2 |
3 |
4 |
5 |
6 |
7 |
8 |
9 |
10 |
11 |
12 |
13 |
14 |
15 |
16 |
17 |
18 |
19 |
20 |
21 |
22 |
23 |
24 |
25 |
26 |
27 |
28 |
29 |
30 |
31 |
|
|
CC Advertisers
|
|

08-14-2011, 07:08 PM
|
 |
CC Member
|
|
|
Join Date: Apr 2005
Location: Tucson,
AZ
Cobra Make, Engine:
Posts: 5,391
|
|
Not Ranked
Welding Aluminum - Questions/Tips
Hey all
I've been fooling around with welding aluminum w/o much good result. I wondered if someone could give me a couple tips on what I'm doing wrong.
I do have a fair amount of experience welding but I haven't tried welding aluminum since high school. And then, it was using a TIG welder.
And that was a LONG time a ago!
I am using my Lincoln MIG, converted to the aluminum set up but not a spool gun. It has Argon gas and .030 filler. I'm running about 25 SCFH of Argon.
The aluminum is cleaned with a stainless pad.
What's happening is the filler burns before contacting the surface, balls up and falls to the surface. I've tried faster wire speed but it then burns through. More amperage, less amperage, more gas, less gas. If I increase the wire speed and the amperage way up, I can get a bead going but it burns through after about an inch. I'm moving it along (pushing) fairly fast as compared to welding steel, so I don't think that's the issue.
Any ideas?
Larry
__________________
Alba gu brąth
|

08-14-2011, 07:35 PM
|
 |
CC Member
|
|
|
Join Date: Jul 2005
Location: Bartlett,
Ill
Cobra Make, Engine: Everett-Morrison LS1
Posts: 2,448
|
|
Not Ranked
tig it unless you have that very high dollar set up like they use welding radiators
|

08-14-2011, 08:46 PM
|
CC Member
|
|
|
Join Date: Jan 2005
Location: Hillsboro,
OR
Cobra Make, Engine: Scratch built CSX style frame, Carbon fiber body, 393 Stroker, T-bird IRS, T5
Posts: 1,623
|
|
Not Ranked
I used my mig for the same aluminum welding, using aluminum wire. This was my first time welding aluminum but I had gotten some advice from this forum so I figured I had someone to blame it on if it all went wrong......
I found out you really need to move much faster than you think you do and your temp has to be adjusted just about perfectly. I had to stop about every 3-4 inches of weld and clean the aluminum again and again to keep a clean weld surface or it just wouldn't lay down a decent bead. Also, your joint has to be very tight or you'll burn through at the gaps every time. Once I got the hang of it, though, it went pretty well and I saved myself having to buy a new sheet of . 080 aluminum.
|

08-15-2011, 12:29 AM
|
 |
CC Member
|
|
|
Join Date: Jun 2009
Location: Sydney,
NSW
Cobra Make, Engine: RCM, Jag front and rear, LS3
Posts: 1,640
|
|
Not Ranked
Im no expert, but can achieve a reasonable weld with mig on Al.
You need to move fast and have the wire feed super fast. Al heats up really quickly (hence why it is used as a heat sink). You will find it working perfectly and then all of a sudden you blow through. Depending on the thickness i do about 12inch lengths.
You also need to push the weld and keep it at a bit more distance then you would with mild. This is important and may be your problem that you are holding the tip too close. You are trying to achieve a spray transfer rather than the conventional weld pool.
It shouldnt be too hard, i tought myself in a couple of hours just messing around with different settings.
Last edited by Zedn; 08-15-2011 at 04:19 AM..
|

08-15-2011, 04:17 AM
|
 |
Senior Club Cobra Member
|
|
|
Join Date: Sep 2000
Location: Holderness, NH, US of A,
NH
Cobra Make, Engine: CSX 4772 old iron FE
Posts: 5,499
|
|
Not Ranked
I found a big difference in performance of one brand wire versus another. It is tricky to keep the weld the same as the start because of the heat dissipation. You might try a preheat. The other big difference I found was a steep push angle, 15 deg off the vertical. I was almost ready to give up and it clicked for me. I used a spool gun and have since got myself one I've found it so useful.
|

08-15-2011, 05:20 AM
|
 |
CC Member
|
|
|
Join Date: Feb 2009
Posts: 1,690
|
|
Not Ranked
Besides all the above, I found pushing the welding handle instead of pulling it works a lot better.
|

08-15-2011, 07:30 AM
|
 |
CC Member
|
|
|
Join Date: Apr 2005
Location: Tucson,
AZ
Cobra Make, Engine:
Posts: 5,391
|
|
Not Ranked
Thanks guys! I'll try the steeper angle. I think the gun would be money well spent. Three times, the aluminum wire kinked just past the drive wheel and I had to undo it.
How much gas flow are you all using?
Larry
__________________
Alba gu brąth
|

08-15-2011, 08:05 AM
|
 |
CC Member
|
|
|
Join Date: Apr 2005
Location: Tucson,
AZ
Cobra Make, Engine:
Posts: 5,391
|
|
Not Ranked
Thanks guys! I'll try the steeper angle. I think the gun would be money well spent. Three times, the aluminum wire kinked just past the drive wheel and I had to undo it.
How much gas flow are you all using?
Larry
__________________
Alba gu brąth
|

08-15-2011, 08:47 AM
|
 |
Senior Club Cobra Member
|
|
|
Join Date: Sep 2000
Location: Holderness, NH, US of A,
NH
Cobra Make, Engine: CSX 4772 old iron FE
Posts: 5,499
|
|
Not Ranked
Hey Larry if you don't use a spool gun you want to close the gap up if you can right after the rolls and use a teflon liner in your torch cable. Your welding chart will tell you where to start on flow. You don't mention the thickness of what you're welding. I would try about what you had 25 - 30 cf/h. Also keep the torch away from the puddle about 3/4". Let us know how it works for you, we like pictures ;-)
|

08-16-2011, 11:59 AM
|
 |
CC Member
|
|
|
Join Date: Apr 2005
Location: Tucson,
AZ
Cobra Make, Engine:
Posts: 5,391
|
|
Not Ranked
Pictures! Can I post steel weld pics instead? I'd rather not embarrass myself in front of the whole world!
Larry
__________________
Alba gu brąth
|

08-16-2011, 12:37 PM
|
 |
Stolen Avitar
|
|
|
Join Date: Oct 2004
Location: Brunswick,
GA
Cobra Make, Engine: BDR 1311 428PI
Posts: 3,044
|
|
Not Ranked
Larry, they won't be any worse than mine and I have a spool gun!
Steve
|

08-16-2011, 06:29 PM
|
 |
Senior Club Cobra Member
|
|
|
Join Date: Sep 2000
Location: Holderness, NH, US of A,
NH
Cobra Make, Engine: CSX 4772 old iron FE
Posts: 5,499
|
|
Not Ranked
Not after all this good juice on the subject, pay your dues Larry!
|

08-16-2011, 09:33 PM
|
CC Member
|
|
|
Join Date: Feb 2003
Location: Plymouth,
MA
Cobra Make, Engine: MidStates, 351C, 4spd, 9"
Posts: 392
|
|
Not Ranked
Hi Larry,
I recall when reading my Lincoln manual (insert chuckle here.. guy reads manual 'news at 11'..) That the recommendation for the spool gun comes from a performance standpoint, whereas the rollers have a tough time pushing the ally through the hose w/o often damaging the wire and fouling the arc performance. The ally setup kit for it has a new liner for your torch hose (as Nick mentioned) and ally rollers. What are you welding by the way... that's another bag o' worms.
Mike.
__________________
"It's not about getting from point A to point B. It is the point"
-J. James
M. Krause
1.508.944.3368
|

08-16-2011, 10:51 PM
|
 |
CC Member
|
|
|
Join Date: Apr 2005
Location: Tucson,
AZ
Cobra Make, Engine:
Posts: 5,391
|
|
Not Ranked
Hey Mike
I have it set up for aluminum with the sleeve but even with it, I'm finding that the AL wire gets kinked feeding into the sleeve. It gets worse the faster I have the feed rate and I'm finding the rate needs to be fast. I've been checking online for spool guns and think that's the way to go.
Right now, I've just been fooling around with aluminum scrap I have laying around. About .080 I think or something around that.
You're cruel Nick!
Larry
__________________
Alba gu brąth
|

08-17-2011, 04:13 AM
|
 |
Senior Club Cobra Member
|
|
|
Join Date: Sep 2000
Location: Holderness, NH, US of A,
NH
Cobra Make, Engine: CSX 4772 old iron FE
Posts: 5,499
|
|
Not Ranked
Larry I think you're trying to get going on material that's too thin. My recommendations are not to MIG ally thinner than 1/8". I would at least set it up on something thicker. I just got a spool gun recently (as I couldn't bear to borrow one anymore) and I have been using it quite a bit. I didn't see the picture yet..........
|

08-17-2011, 05:11 AM
|
 |
CC Member
|
|
|
Join Date: Jul 2010
Location: Augusta,
MO
Cobra Make, Engine: Sold ERA FIA 2139, 331 Weber IDF
Posts: 279
|
|
Not Ranked
After welding hundreds of meters of bead on the above; I found that you really can not have too much gas flow, at some point it just becomes wasteful though. Are you welding outside in the wind or in the path of a fan? Good luck then, because the wind easily blows away your gas shield. A spool welder is your best bet if your going to do a lot of welding, however, if you keep your cable as straight as possible, you can get by with what you have. Good weld is definitely about having your feed speed and voltage correct, if your feed is jerky, it is going to look like crap. Thin gauge stock that you are welding, you will have to weld in short beads, you will find warpage a problem also. Have fun
|

08-17-2011, 07:51 AM
|
 |
CC Member
|
|
|
Join Date: Apr 2005
Location: Tucson,
AZ
Cobra Make, Engine:
Posts: 5,391
|
|
Not Ranked
Holy Cow wolf, now that's a project!
Thanks for the advice.
Larry
__________________
Alba gu brąth
|

08-18-2011, 07:53 AM
|
 |
CC Member
|
|
|
Join Date: Feb 2007
Location: Colorado Springs,
CO
Cobra Make, Engine: Backdraft, supercharged Coyote
Posts: 2,434
|
|
Not Ranked
Do you need to use gas? What gas do you use?
I don't use gas with my MIG welder, but I can. I know on steel you get a cleaner weld, but so far I havn't wanted or needed to mess with gas.
__________________
.boB "Iron Man"
NASA Rocky Mountain TTU #42
www.RacingtheExocet.com
BDR #1642 - Supercharged Coyote, 6 speed Auto
|

08-18-2011, 09:04 AM
|
 |
Stolen Avitar
|
|
|
Join Date: Oct 2004
Location: Brunswick,
GA
Cobra Make, Engine: BDR 1311 428PI
Posts: 3,044
|
|
Not Ranked
For Ally use argon. For mild steel I use a 75/25 mix of CO2/argon but I do know people who use straight CO2 for steel as well.
|

08-19-2011, 07:22 AM
|
Senior ClubCobra Member
|
|
|
Join Date: Feb 2006
Location: Northern,
Ca
Cobra Make, Engine: LA Exotics
Posts: 1,037
|
|
Not Ranked
I found MIG aluminum welding to be very difficult (no spool). I never got the hang of it. I'm guessing the spool would go a long way in making it easier.
I now use TIG. The thing that is most important with aluminum is cleanliness, cleanliness, and cleanliness. The aluminum has to be absolutely clean and free of oxide. Wipe it down with alcohol to get rid of any oils and then use your stainless pad. Make sure the stainless pad is also clean. If you don't see a nice shiny pool; if you see a non-shiny skin form, the aluminum is not clean or you have not scoured off the aluminum oxide. Aluminum forms an aluminum oxide skin almost immediately. The stainless pad should remove it. But it will form again very quickly. The AC current will clean off some of the oxide, but if it gets too thick, it won't do the job and you will not see a nice shiny pool, but rather see a skin form on top with the liquid aluminum underneath. If that happens, stop and re-scrub the aluminum.
|
Posting Rules
|
You may not post new threads
You may not post replies
You may not post attachments
You may not edit your posts
HTML code is Off
|
|
|
All times are GMT -7. The time now is 06:53 AM.
Links monetized by VigLink
|